Acrylic Perspex
PLEXIGLAS®
Acrylic is one of the world’s most versatile and highest quality plastics. Available in solid sheets, blocks and tubes with unbeatable resistance to UV light and weathering, combined with durability. The products are either clear and brilliant or available in a large number of transparent, translucent and opaque and fluorescent colours.
With excellent optical clarity and weatherability at only half the weight of glass, acrylic is suitable for a wide variety of applications in the display, fabrication and glazing industries.
Acrylic (also known as Perspex or PLEXIGLAS®), is a popular material for may applications. In its purest form it is completely clear and transparent and yet much lighter and safer than glass. It’s UV protection and high weather resistance ensures that the material looks new, even after many years of use.
- Up to 17 times stronger than glass
- Safer than glass – does not shatter
- 30 year guarantee of not yellowing
- Excellent chemical resistance
- Higher light transmission than glass
- Easy to process – thermoforming, bending, gluing, milling
- Easy to handle, install & clean
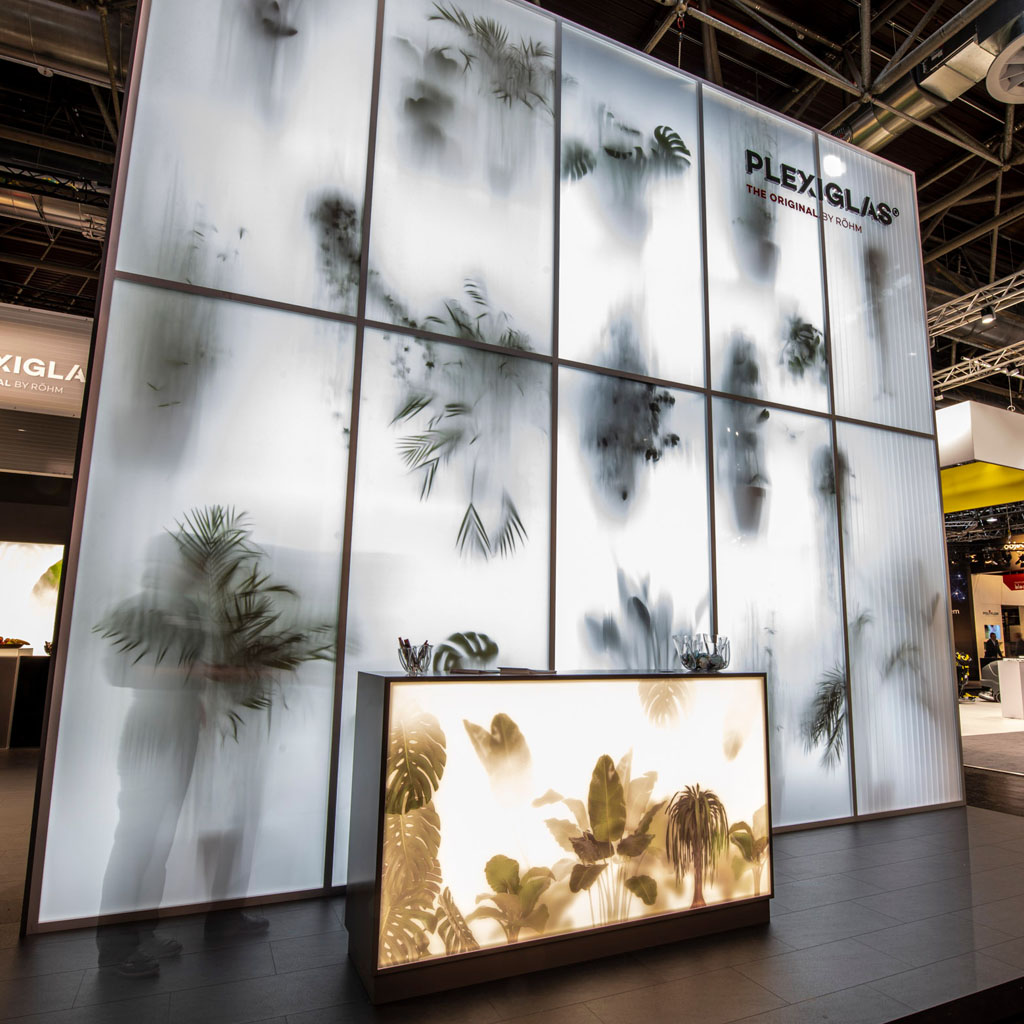
Access Plastics is the official distributor of PLEXIGLAS® in Ireland. What exactly distinguishes Röhm’s branded acrylic from all the other acrylics in the world? PLEXIGLAS® is the original, invented in 1933, and a brand name of Röhm GmbH. With remarkable pioneering spirit, a passion for innovation, and decades of experience, the original material, a transparent sheet, has now evolved into an entire product family.
Product Range
PLEXIGLAS® GS/XT
CAST & EXTRUDED SHEET.
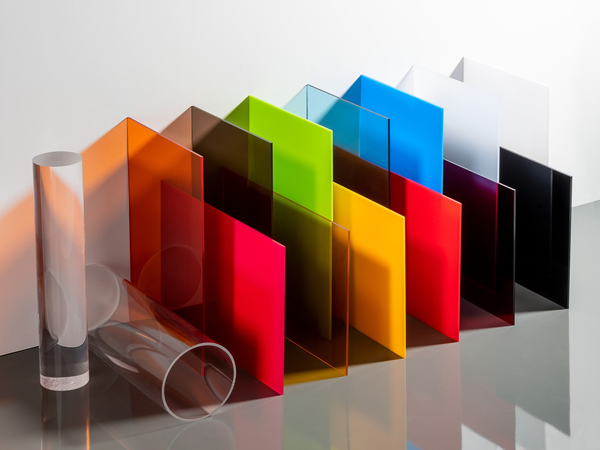
PLEXIGLAS® Hi-Gloss
HIGH GLOSS SOLID SHEETS
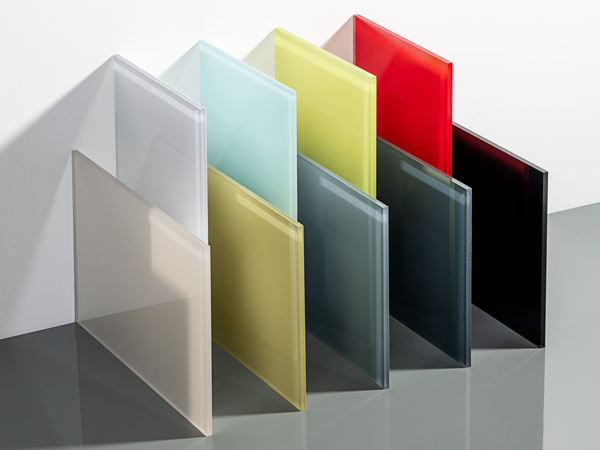
PLEXIGLAS® LED
MAXIMUM TRANSMISSION FOR MAGICAL LIGHTING
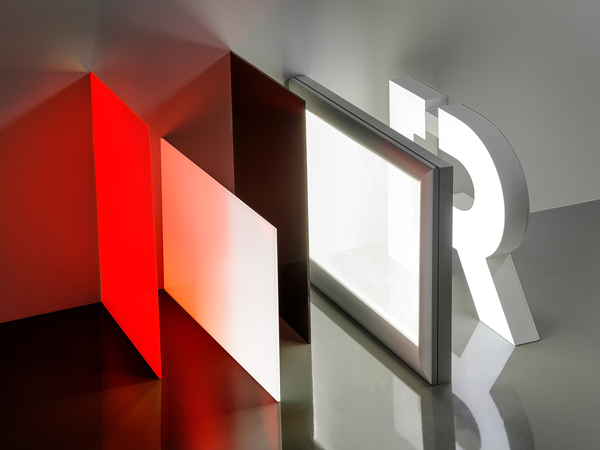
PLEXIGLAS® LED offers a new dimension of light. It consists of a specialty PMMA sheet combined with LEDs, for efficient lighting applications including, edge lighting, side lighting and backlighting..
PLEXIGLAS® SATINICE
COMBINES ELEGANCE WITH FUNCTIONALITY
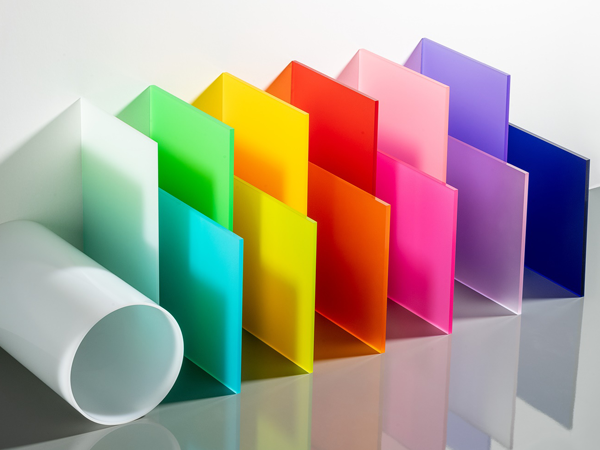
PLEXIGLAS® PROTERRA
RECYCLED ACRYLIC GLASS
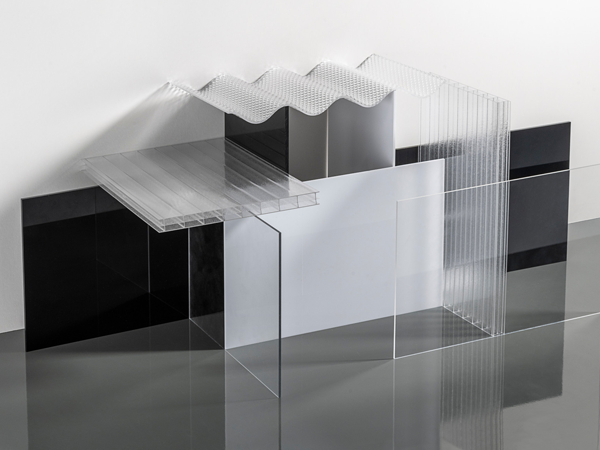
PLEXIGLAS® RODS & TUBES
FOR LIGHTING & ARCHITECTURE
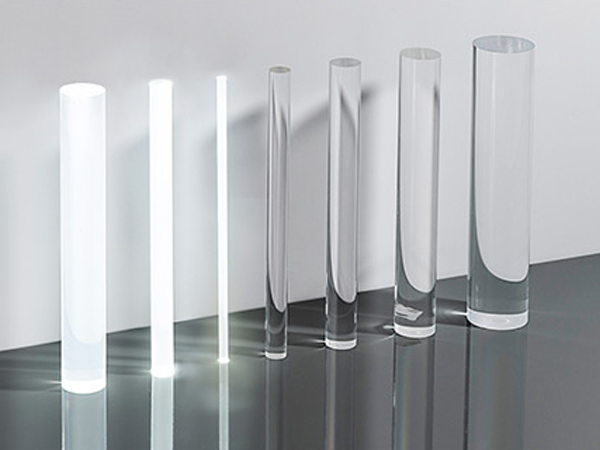

High Optical Clarity & Exceptional Durability
Sheets—also commonly referred to as panels—and blocks made of PLEXIGLAS® are the starting point for a wide variety of potential applications. Thanks to their considerable durability and resistance to UV and weathering, sheets and blocks can be used both in interior and exterior applications .
17 times stronger than glass with only half the weight
Acrylic sheets have good resistance to UV radiation. Won't yellow or degrade when exposed to sunlight.
Acrylic sheets can be easily cut, drilled, and shaped with standard tools & can be bent into complex shapes using heat
Highly transparent, allowing up to 92% of light to pass through
Long service life means that it does not turn yellow or become brittle & retains its high light transmission
Acrylic sheets are much lighter than glass, which makes them easier to handle & transport
Excellent Technical Performance
Withstands temperatures as low as minus 40°C & up to 80°C heat
Good chemical resistance to diluted acids and to alkalis,
Good acoustic insulation properties making it suitable for outdoor sound barriers or indoor partitions
Outstanding fire properties, which are retained throughout its entire lifetime
Is suitable for use with food and is EU and FDA approved.
It is 100% recyclable & can be broken down into its original components to create new products
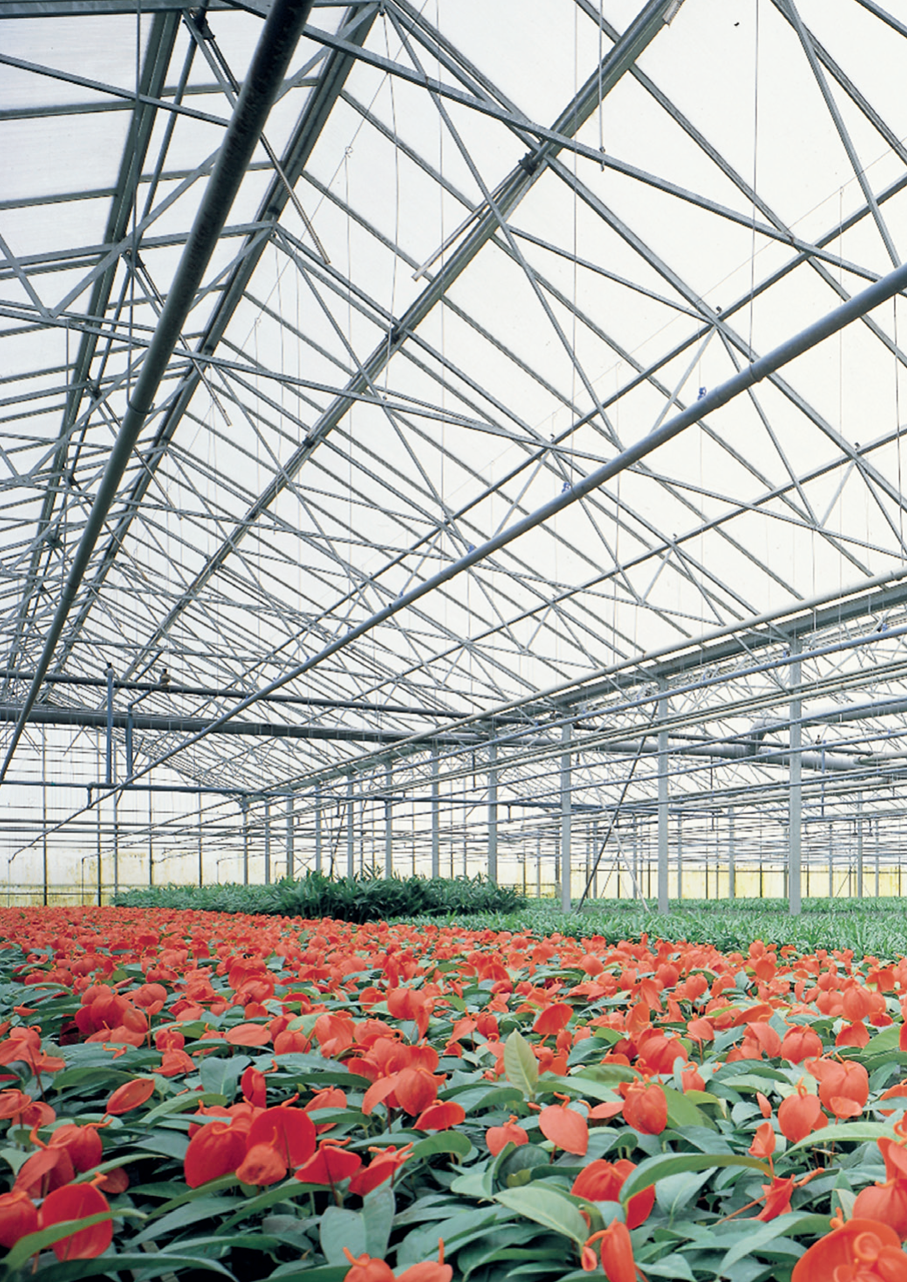
Applications

Home & Garden
Cozy, elegant and versatile: from patio roofs to conservatories, household items to white goods, PLEXIGLAS® is ubiquitous. In outdoor applications, its weather resistance makes it the material of choice, and indoors, it brings light and color to living rooms. Safety is just as important as versatility, light weight and transparency.
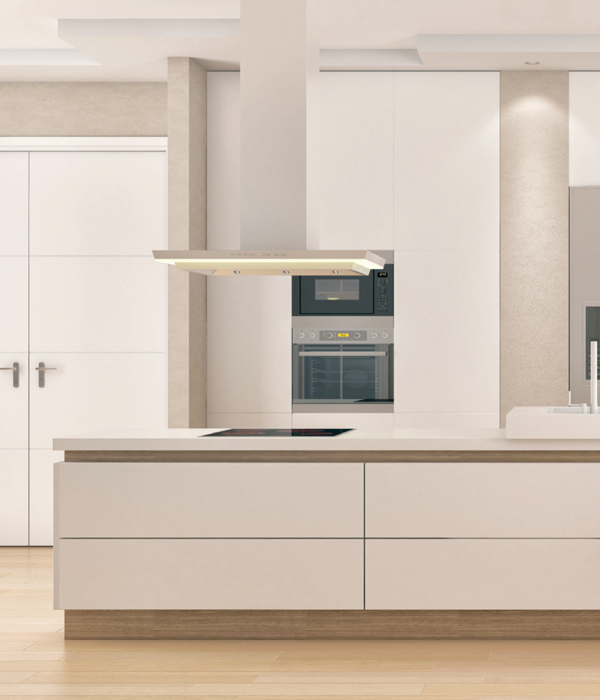
Interior Design
PLEXIGLAS® is the perfect material to draw attention, create a striking effect and stand out from the crowd. Combined with light, it offers endless scope for design in furniture, furniture profiles and kitchens. The material’s easy-care surface that is warm to the touch contributes to all-round comfort.

Visual Communication
Luminous advertising messages make public spaces more lively and colourful. PLEXIGLAS® has been one of the leading materials for visual communication, trade fair construction and shop fitting for decades. It diffuses light evenly, offers a wide variety of colours and shapes, is robust and very durable.
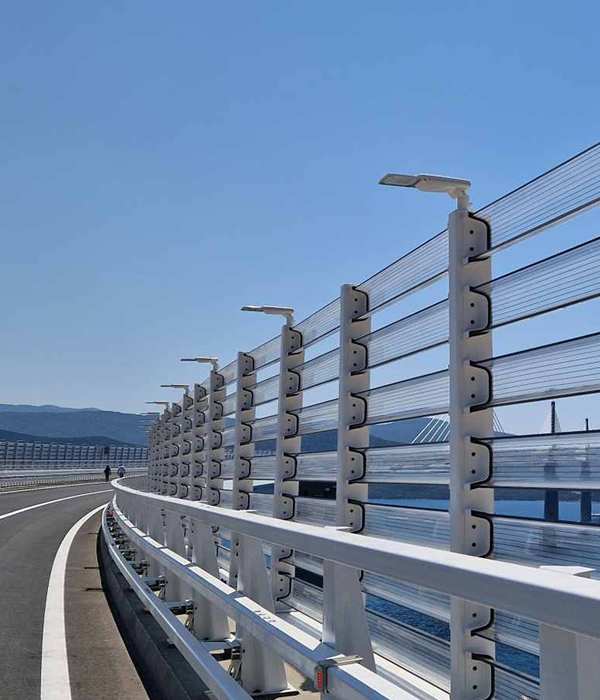
Noise & Wind Protection
The global traffic volume continues to grow – and so too does noise pollution for people who live close to roads and rails. Transparent walls made of PLEXIGLAS® protect against noise without blocking views of the surrounding area. Acrylic sheets offer effective noise and wind protection, high light transmission, extreme weather resistance, exceptional stability and good environmental compatibility.
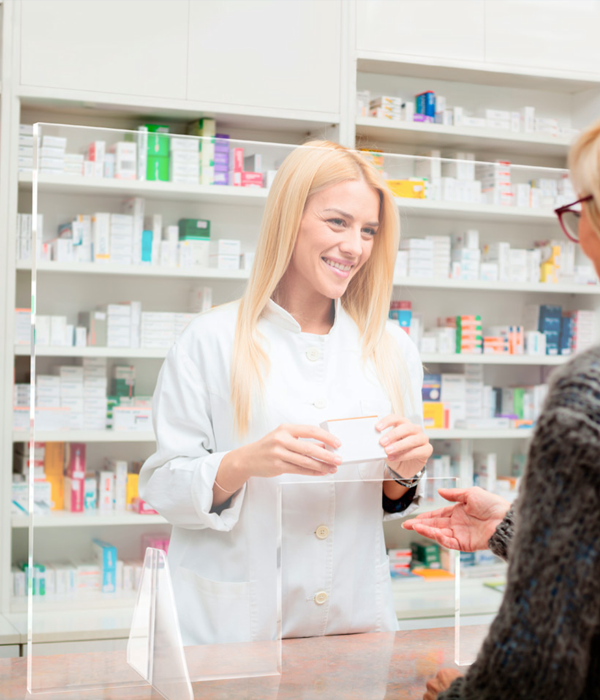
Hygiene Protection
PLEXIGLAS® products with smooth, non-porous surfaces are generally suited for areas with strict hygiene demands as they are easy to clean and can be disinfected with suitable products. Protecting our health has become critical in all areas of public life and acrylic sheets are ideal for hygienic partitions and enclosures. for retailers, hotels, restaurants, health centres, schools, public authorities, and offices.

Pools & Aquariums
PLEXIGLAS® pools and aquarium glazing provides excellent long-term performance. With the crystal-clear transparency of entire side walls or even the floor, PLEXIGLAS® add a spectacular dimension to the swimming and underwater experience. The excellent formability, extreme stability and decades of durability of acrylic make almost anything possible and opens up countless opportunities for setting architecturally impressive designs.
30 YEAR GUARANTEE
Be on the Safe Side with PLEXIGLAS®
UV radiation can cause dramatic changes in most plastics. They may turn yellow or brown, and become unsightly. When new, transparent plastics all look more or less the same. The nasty surprise often comes a few years later,. Products that contain natural UV protection throughout the material are best equipped. PLEXIGLAS® with the special NATURALLY UV-STABLE technology has such natural protection.
- PLEXIGLAS® DOES NOT YELLOW VISIBLY
We guarantee that PLEXIGLAS® sheets will show no visible yellowing for 30 years. - PLEXIGLAS® RETAINS HIGH LEVEL OF TRANSPARENCY
We guarantee that PLEXIGLAS® sheets in Clear grade will retain a high level of light transmission for 30 years. - PLEXIGLAS® RETAINS ITS COMBUSTION BEHAVIOUR
We guarantee that PLEXIGLAS® will retain its fire behaviour even after 30 years of weathering. - PLEXIGLAS® GUARANTEES
Apart from the 30-year guarantee, we provide a number of other guarantees that refer to the special properties of various grades
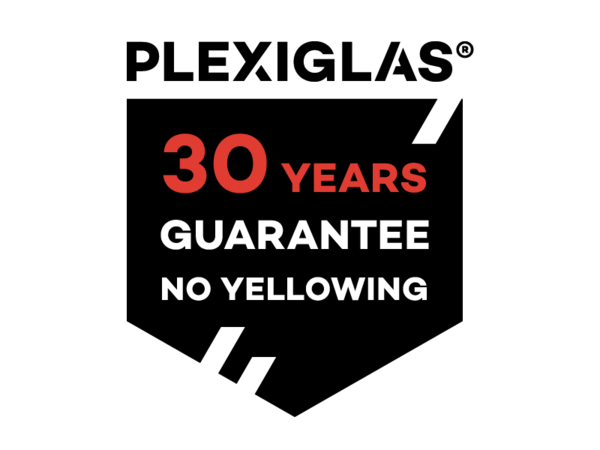